制作法
制作法
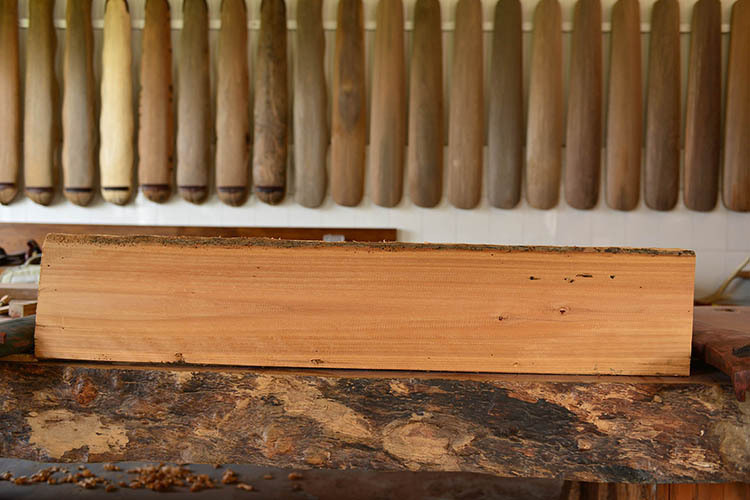
◆Selection of materials:
Traditionally, when people select materials, they differentiate yin from yang. While tong (Chinese parasol) wood is considered yang, zi (Chinese catalpa) wood is treated as yin. When yin matches yang, harmony is obtained. It is recorded in Dong Tian Qing Lu Ji (Dong Tian Qing Lu: A Collection of Essays) that “The top board produces the sound while the bottom board vibrates the sound. If the bottom wood is not firm, the sound must be diffused.” The wood selected can be old or new because, while old woods are the priority, there are old woods that may produce poor sound. On the other hand, new woods may have the potential to produce beautiful sound. Therefore, the selection of woods depends on sound quality. The age of the woods shouldn’t be the determining factor. Whether it is old or new wood, straight or crooked, it is good wood as long as the wood used for the top board is yang wood and the wood used for the bottom board is yin wood, and as long as the completed qin conforms to the “nine virtues” of qin.

◆Visual inspection of materials:
Whenever I start making a new qin, I first study the wood for some time, either by holding it in my hand or putting it on the work-bench, inspecting the look of the wood and evaluating its sound. Before I actually start shaping the wood, the shape of the qin is already in my mind. Only after I have carefully inspected the yin and yang of the wood, weighed what style of qin to be made and have an idea what kind of lacquer and accessories will be used, I would then start the process. If, like some qin-makers who have no patience and are only interested in getting immediate results, one starts the shaping process without evaluating the woods, how can one expect to get such great qins like jiaowei (scorched tail) and yuqing (sonorous stone) the sound of which drifts in the clear breeze and over flowing waters?
The inspection of the wood should be done professionally. This is the first step in qin-making and therefore must be given due attention. In the old days, people would either prepare a cup of tea or a pot of wine, sipping it slowly in serenity and carefully going through various considerations. Then one would not regret making any possible mistakes. You reap what you sow. Every effort made at the preparation stage pays off in the end.
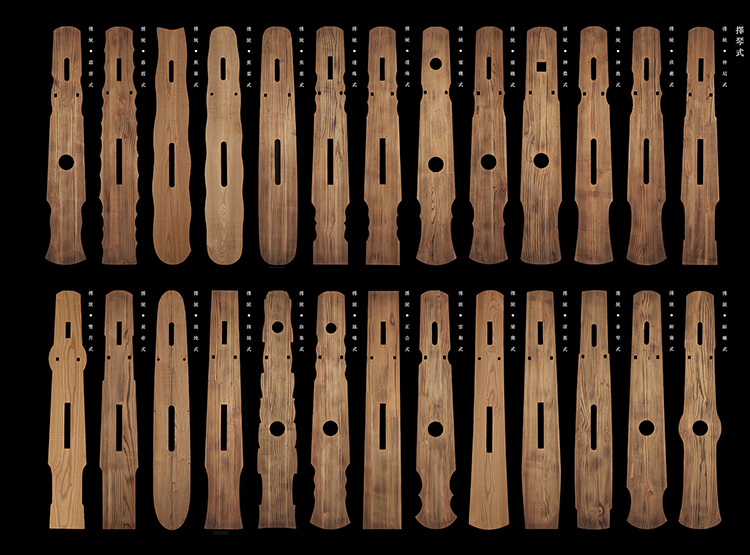
◆Selection of styles (forms):
As far as qin styles (or forms) are concerned, it is believed that Zhongni (based on Confucius style name) and Liezi are the only two ancient styles. The rest of the styles were all created later. There are several dozen styles created since the Tang Dynasty. Tai Gu I Yin (Inherited Sound from Antiquity, which doesn't exist any more) by Tian Zhiweng of the Southern Song Dynasty is the earliest book that has recorded qin styles. A total of 38 styles are recorded in Tai Yin Da Quan Ji (Complete Book of the Sound from Antiquity) by Yuan Junzhe of the early Ming Dynasty, while in the books published later on, such as Feng Xuan Xuan Pin, Wenhui Tang Qinpu (Wenhui Hall Tablature Collections), and Gu Yin Zheng Zong (Authentic Tones from Antiquity), the number of styles has increased to more than 40. Wuzhi Zhai Qinpu (Tablature Collections of Wuzhi Hall) of the early Qing Dynasty has recorded more than 50 styles. Nowadays, more styles have been created by contemporary qin makers. Each maker chooses the styles of his/her own preference.

◆Design:
With the qins I make, I have selected 28 traditional styles, 18 self-created styles, and six imitations of traditional styles. With traditional styles, even though they are based on original models, each one may reflect the qin-maker’s personal interpretations and idiosyncrasies. Some may have beautiful curves that draw our undivided attention; others may have such a magnificent and grand look that, once picked up, we can’t bear to put them down. Of course, there are also others that either have discordant curves or look ugly. With such qins, even if their sound is passable, their lack in appearance means they cannot be called perfect qins. The design of various styles of qins varies over the years. Now and then, there are some new styles, prized by people of the day and then criticized later on. I think new qin styles are a mirror of the aesthetic judgement of the day. We can model after traditional styles and yet not be confined by them; we can create new styles but not for the sake of creating new styles. The new styles must be inclusively based on traditional aesthetic philosophy, in achieving the resemblance, in managing the positions of various parts, and in exhibiting a vivid charm. Besides, it is not appropriate to arbitrarily change the structure of classic styles, which have reached a certain level of perfection. It is not appropriate to add fancy colors and engrave gold into the instrument, which will distort the music of classic antiquity.
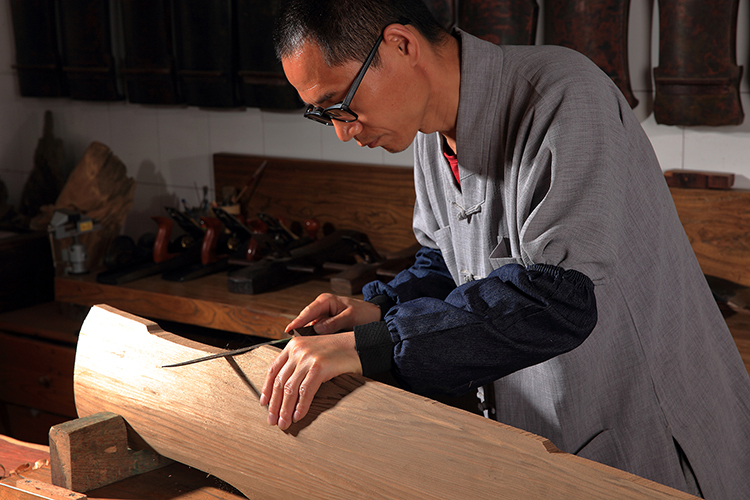
◆Model making:
Once the styles are selected and the diagrams drawn, it is time to use the axe to create the model after repeated inspection to ensure that nothing is wrong. There are two ways to create the models: firstly, by using traditional tools to create the model entirely by hand. It is a quiet and peaceful as well as enjoyable process. Though it might take a longer time, it is also an attitude towards life; secondly, by using power tools, such as band saws, power planers and angle grinders. They are convenient and efficient without losing precision. But the whole process is noisy and distracting, not something that I like. Although I don’t like it personally, I don’t want to disparage it. If there are people in the field who have good skills and the commitment of a good craftsman towards what they do, I don’t see any reason why they can’t use power tools instead, for saving time and effort, for lowering the cost and for mass production. It is good for popularizing qins.Compared to the making of traditional furniture, the carpentry skills involved in the making of qin models are considered rudimentary. However, one should not be careless even if the skills are basic. Good craftsmanship lies in the detail of every step of the process, whether it is wielding the axe or pushing and pulling the saw. There are over 100 steps in the whole process. If attention is given to every step, good products are a natural result. In shaping the models, whether one decides to do it by hand or by machines is a personal preference or sometimes it is a selected choice constrained by conditions. There is no one right answer. The ultimate goal is to produce good qins.
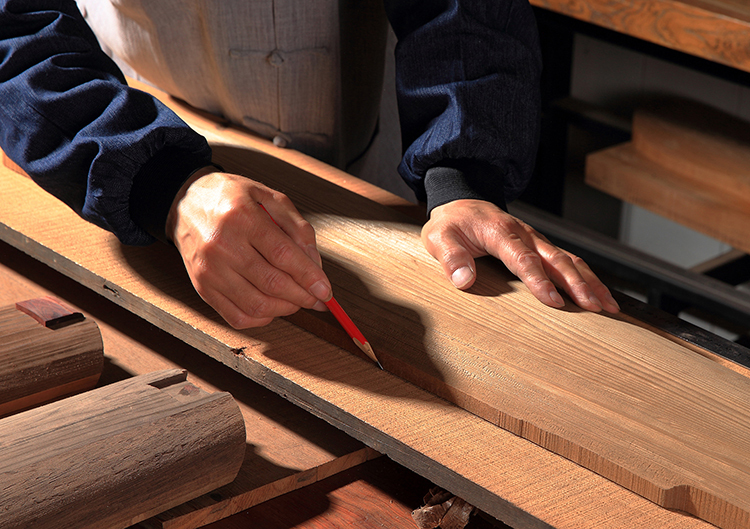
◆Selection of bottom board:
Once the preliminary shape of the top board is ready and the curves on the top and underneath the top board are basically carved, knock on the wood with your fingers and choose the appropriate bottom board according to the color of tone you are aiming for. The selection of bottom board materials depends on the desired tone you are after. There are no fixed rules. There is no exact science in the selection of the grains and the yin and yang of the bottom board wood. The wrong choice of wood might regrettably affect the natural sound of the top board. Or one can choose whatever bottom board is available without being too picky and let fate decide the outcome. Of course, whether one can get a good qin by this method in the end is entirely up to fate. Besides, the thickness of the bottom board, the positions and specifications of the sound holes (dragon pool and phoenix pond) are determined by the sound produced by the top board. There are no unified rules, either. In short, if one wants to come up with a qin that can be passed down through generations, one must first of all have a well thought-out plan regarding the technical skills to be used and the layout design in the same way as a Chinese painting artist has everything in his/her mind before the painting starts. In doing so, he/she is not confined by one particular way whether it is fine brushwork or not. However, if the accomplished ones can achieve what they desire, the completed product will look as if it is created by nature. How can such naturally crafted masterpieces be made according to one standard?
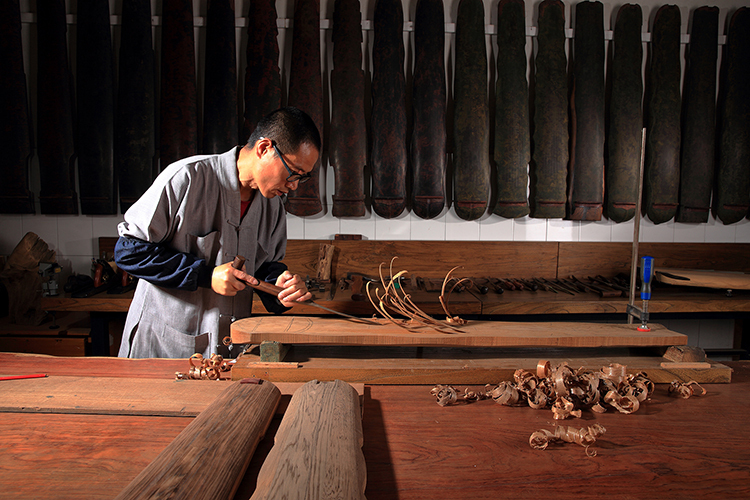
◆Hollowing the top board
The qin cavity determines the size of the resonance chamber which in turn affects the quality of the timbre. That is why qin makers long ago felt that the quality of the sound is determined 30% by the wood used and 70% by the technical skill of the maker. Therefore, the cavity of the sound board must not be too deep nor too shallow; the sound absorbers must not be too high nor too low; the bottom board, the top board, the head and tail of the qin must vary in thickness; the thickness of the sides and the center must also be different. However, I don’t think I should give one set of specific parameters here, as various types of wood differ in nature and their sound quality varies. Besides, the measurements used over the years are not the same, either.
In hollowing the inside of the sound or top board, one should start with the forehead and move down to yueshan (bridge) and, from there, down further towards longyin (dragon’s gums). And then, one can further move down to the neck, shoulder, waist and the tail. In doing so, one should use the bottom board to measure the progress and ensure to reserve excess wood, about 3mm, for further adjustment. In the dozen years of my qin making experience, I have come across many times very soft wood which can produce loud and open sounds. But they tend to be empty, lacking a certain degree of substance. After repeated trials, I have learned to increase the thickness of the pad in the cavity, transforming the empty sound into something rich and serene. The qins I have made so far by using such a method have all been good. That is why this method is given the name baina pad, for the purpose of tuning the tone rather than for novelty.
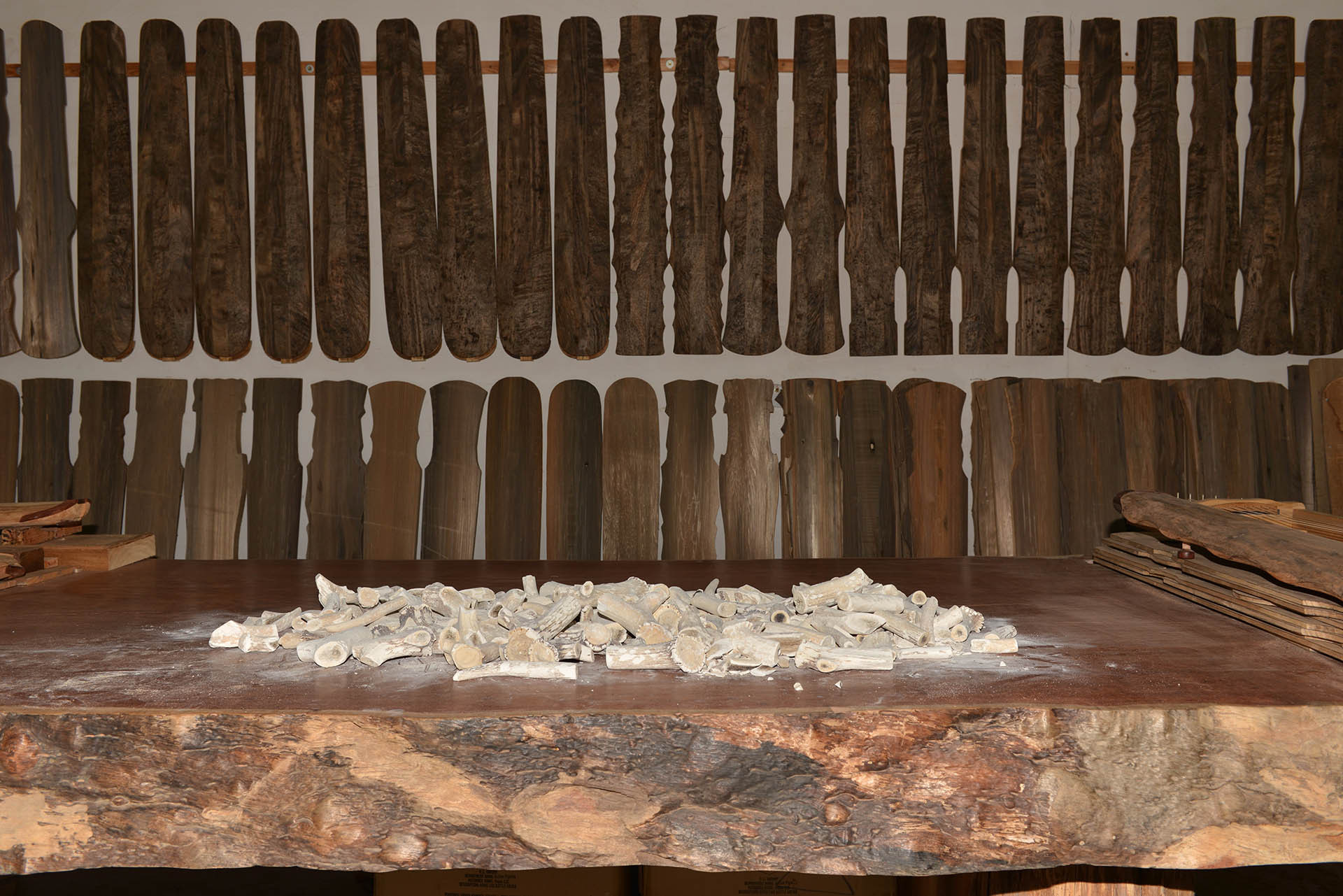
◆Stablization
Once the rough cast is made, the qin must be hung up on the wall for between six months to a year for stabilization, until the internal stresses are totally removed while the qin is being air-dried in the shade. Sceptics often laugh at such a practice, thinking it is unnecessary. They forget that all creatures in the universe have their own inherent nature. So does wood. That is why it can produce the natural sound of heaven and earth. Others change the nature of wood through modern modification technologies, causing wood fibre to harden and stagnate. It is like the use of chemical fertilizer in farming. While it increases production, the harvest lacks in taste. Su Shi, a well-known Chinese poet of the Song Dynasty, once said, “With qins less than 100 years old, the rawness of the tong wood (Chinese parasol) is not entirely gone. Therefore, the various tempo or speed of its sound corresponds with the changing weather. Nowadays, people sometimes cure tong (Chinese parasol) and zi (Chinese catalpa) woods by soaking them in water and then smoke-dry them over fire or under the sun. But these methods compare poorly with the natural curing process.” That is why I choose the natural curing method (drying in the shade) by hanging the un-lacquered qins on the wall for as long as three to five years. Although it takes a longer curing time, since the rough cast is firm, the sound becomes robust and the tone and melody perfect, the qins can be used to play the great sacred Buddhist music in the bamboo groves on moonlit nights.
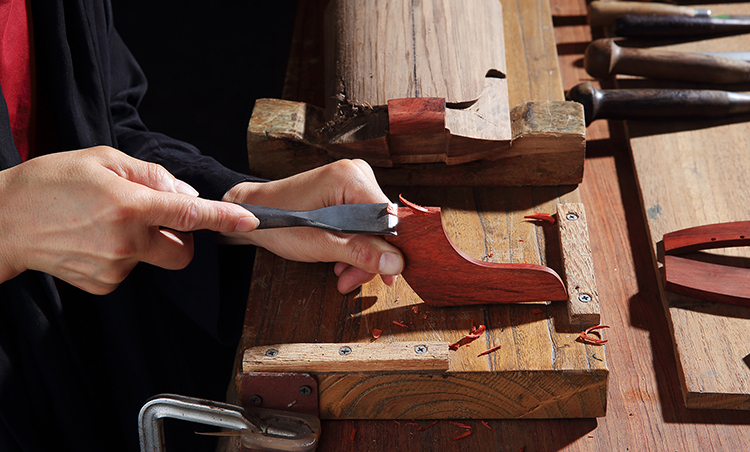
◆Pre-installing accessories
Once the un-lacquered qin has dried in the shade and the qin body has been finely shaped, accessories should be pre-installed for tuning. While this step is included more for tuning, the un-lacquered qin body with its accessories installed has its own beauty as well.
Red sandalwood, rosewood or other precious woods are usually the top choices for accessories. According to Gu Yin Zheng Zong (Authentic Tones from Antiquity), jade was prized as the most precious for making pegs in the old days, followed by agate, crystal and ivory. I only use red sandalwood, sawed off and prepared from bigger pieces of wood. With old red sandalwood, the cracks, rotten sections and woodworm damage must be removed first. All the guanjiao pieces (ceremonial caps) are made by cutting thick materials in half (book-matched) so that they have beautiful symmetrical wood grain.
The accessories to be pre-installed must be selected according to the qin styles and shapes. The shape of the accessories must be considered as well, and then made according to the qin styles to add beauty to the qin. The size of the accessories should match the qin and be nestled snugly against the qin as seen fit. Care must be given to every step of the process, from measuring, positioning, drawing the lines and shaping, aiming at a snug fit with no obvious gap between the accessories and the qin body. There are people in the field who use lacquered paste to fill the gap due to their own careless mistakes made during the process. But the joints are bound to crack open with the change of seasons later on. Good craftsmanship yields good products. Otherwise, regrettable defects will be found in the instruments.
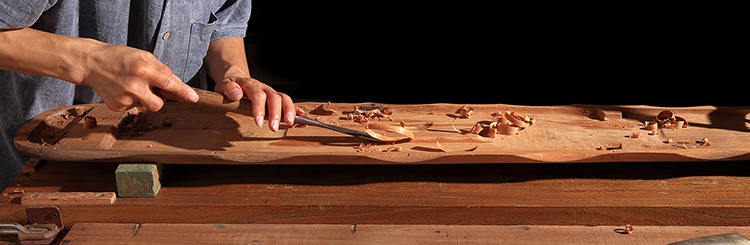
◆Fine-shaping the inside cavity
After the accessories are installed and the tone tested, the belly of the soundboard is fine-shaped to achieve the desired tone quality. When hollowing the inside cavity initially, it is always advisable to reserve some excess wood, about 3mm, for further adjustment. If there is still wiggle room, the excess wood could be thinned by half or completely.
According to tradition, the cavity of qins made in the Song Dynasty is usually 18 to 21mm deep, while the cavity of those made in the Tang Dynasty is 24 to 27mm deep. The cavity of the famous baina qin made by Lei Wei, an accomplished qin maker of the Tang Dynasty, is believed to be as deep as 36mm, according to historical records. Different qin makers have different requests for timbre or tone quality. Therefore, they would make minor adjustments for different styles of qins, including the thickness of the qin body and the depth of qin cavity. People today sometimes argue about the standards. I don’t think it is necessary. The merits and drawbacks in rendering the qin cavity lie in the quality of the tone and the feel of touch.
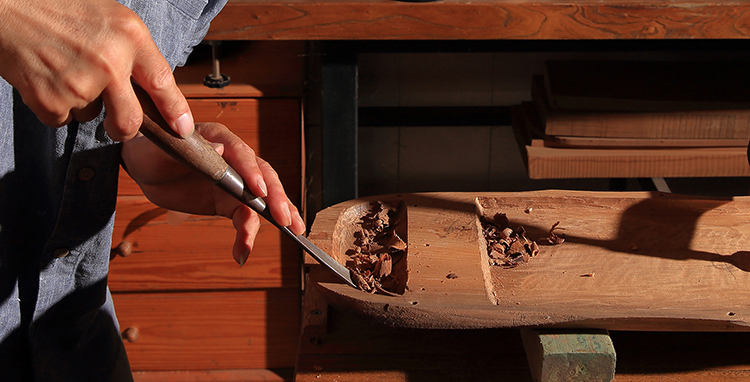
◆Carving the shexue
Shexue, literally “tongue cave”, is a hidden slot inside the qin belly at the head part, more commonly seen in qins made in the Tang and Song dynasties. It helps with the sound production. By Ming and Qing dynasties, fengshe (phoenix tongue) became rare. The forehead of the qin became solid wood. It was recorded in Tai Gu Yi Yin (Qualification of Qin Music) that, “shexue is 39mm deep and about 20mm wide … a piece of wood slot is inserted in it.” The qin styles today differ from those in the old days. The length and the size of shexue are determined by the width of the forehead of the qin. They should be adjusted accordingly so that the tone and melody are serene and sublime, pure and beautiful, just like the harmonious chanting of the male and female phoenix.
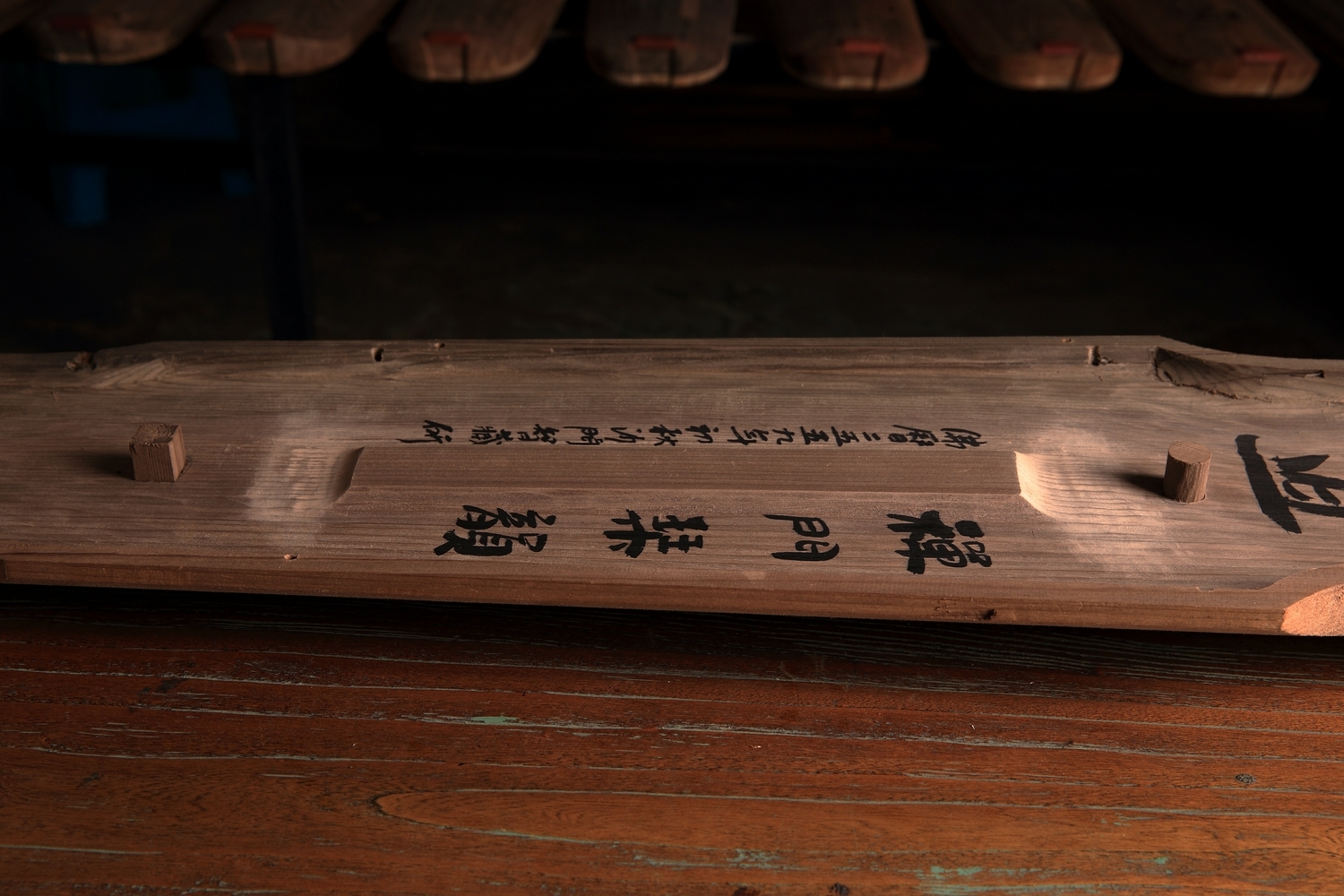
◆Installing pillars of heaven and earth
There is a round tianzhu (pillar of heaven) and square dizhu (pillar of earth) inside the qin cavity below the shoulder part and near the waist, which has been included since the Tang Dynasty. They provide support inside the slot belly. With some old qins, both tianzhu and dizhu are round, in spite of the common traditional belief that heaven is round and earth is square. More recent qins have different shapes and therefore their structures are different, too. I use round pillars of heaven and square pillars of earth, though their size and height differ. The positions vary slightly as well according different qin styles and shapes. But the diameter must be right, not too big, nor too small. If it is too big, the sound tends to be dull with short melody; if it is too small, the sound will be too bright and diffused and the tone and sound are mixed together.
Pillars of heaven and earth are included for dual purposes: firstly, they enhance reverberation; secondly, they provide support so that the top and bottom boards will not be deformed easily. There are new qins in the market that either don’t have pillars of heaven and earth or only have fake ones installed, for the purpose of producing loud and robust sounds, which tend to be diffused and unclear, defeating the purpose of playing the qin. If clarity is sacrificed, one had better stop playing the qin and take to the zheng (or guzheng), another traditional Chinese musical instrument usually with 21 strings. If one wants to find out whether there are pillars, one can knock on the positions where they are supposed to be with a crooked finger. If it sounds solid, there are pillars. If the sound echoes, there are no pillars.

◆相材:
余每斫琴,取材在手,或置于案头,须进行一翻审视端详,以相其表、审其音。未斫之时已卓然成形,观其阴阳向背,度其体形规格,于用漆配料,了然于胸,方始动工。彼斫琴者,若意烦体悖、拙鲁急功,斫琴不论相材,取之即砍,焉得焦尾玉磬扬音于清风流水哉?
斫琴之相材,用方家态度,为斫琴第一步,须十分重视之。彼时,若备上一杯清茶或一壶老酒,于宁静中精斟细酌,度量有加,斫之不悔。所谓种得良因,必得良果。

◆相材:
余每斫琴,取材在手,或置于案头,须进行一翻审视端详,以相其表、审其音。未斫之时已卓然成形,观其阴阳向背,度其体形规格,于用漆配料,了然于胸,方始动工。彼斫琴者,若意烦体悖、拙鲁急功,斫琴不论相材,取之即砍,焉得焦尾玉磬扬音于清风流水哉?
斫琴之相材,用方家态度,为斫琴第一步,须十分重视之。彼时,若备上一杯清茶或一壶老酒,于宁静中精斟细酌,度量有加,斫之不悔。所谓种得良因,必得良果。